摘要 摘要:砂带磨削具有良好的磨削加工性能,采用3种不同磨料砂带对304不锈钢进行了工艺试验,对磨削后工件表面粗糙度及砂带磨损表面形貌进行了观测。讨论了砂带线速度、磨削压力、磨料种...
摘 要:砂带磨削具有良好的磨削加工性能,采用3种不同磨料砂带对304不锈钢进行了工艺试验,对磨削后工件表面粗糙度及砂带磨损表面形貌进行了观测。讨论了砂带线速度、磨削压力、磨料种类对材料去除率的影响。在磨粒磨损理论模型的基础上,揭示了砂带的磨损机理。实验表明,随着砂带线速度和磨削压力的增加,材料去除率增加,碳化硅磨料约为24m/s,锆刚玉及陶瓷磨料约为33m/s时,材料去除率达到最大值。在磨削时间较长时,表面粗糙的大小与接触轮硬度的关系不大。锆刚玉磨料的磨损过程复杂,碳化硅磨料的磨损过程则比较稳定,以摩擦磨损为主。
Test Research on the Abrasive Belt Grinding of 304 Stainless Steel
Abstract: Because belt grinding shows many advantages, process tests of 304 stainless steel were conducted with three kinds of abrasive grain. The surface roughness and the surface topography of belt wear were observed. The influence of belt speed, grinding force and abrasive type on material removal rate were discussed. The wear mechanism of belt wear was revealed based on the model of abrasive grain’s wear. It has been shown that,material removal rate increases with the belt speed and grinding force increasing. The material removal rate reached maximum when silicon carbide abrasive’s speed is 24m /s or zirconia and ceram abrasive’s speed is 33m /s. The surface roughness seems to be independent of the roller’s hardness when the grinding time is long enough. Zirconia’s wear process is complex, thus silicon carbide’s wear is relatively stable dominated friction wear.
引言
304不锈钢具有热稳定性好、耐腐蚀性及耐磨性好等特点,并且具有全面和良好的综合性能,因此被广泛应用在航空、航海、汽车配件、医疗器具等领域[1-2]。随着生产的发展,人们对其加工精度及加工效率的要求也愈来愈高,但是由于其韧性大、导热系数小、弹性模量低等特点,在使用砂轮磨削加工时易产生以下问题:①磨削力大、磨削过程发热加剧;②磨屑易粘附砂轮;③磨屑难以切离、磨粒容易磨钝;④加工表面易产生烧伤和裂纹,表面粗糙度增大,工件表面质量不易保证[3-5]。这些问题在一定程度上限制了304不锈钢的推广和使用。为此,研制性能卓越的不锈钢磨削工具,提高磨削效率与磨削质量,已成为非常迫切的要求。
砂带磨削技术的发展,为解决上述问题提供了一条有效的途径。砂带磨削是一种优质高效的工艺技术。砂带磨削具有磨削、研磨和抛光等多重作用,使得表面加工质量粗糙度小,加工表面发热少,即使干磨也不易烧伤工件,具有“冷态加工”的美誉[6-7]。砂带磨削还具有加工效率高,工艺灵活性大、适应性强等特点,对加工不锈钢有其独特的优势。
本文通过3种不同磨料砂带对304不锈钢进行磨削试验,分析砂带线速度、磨削压力等工艺参数对材料去除率、工件表面粗糙度的影响。借助SEM观察砂带表面磨损形貌,
研究砂带磨损机理,以期提高304不锈钢的加工精度和磨削效率,实现304不锈钢的大规模应用。
1磨粒和加工表面的实际接触时间ts
在磨削过程中,当旧的磨粒磨损后,就不断会有新的磨粒参与磨削,因此参与磨削的磨粒数基本上是不变的。磨粒和加工表面的实际接触时间ts是一个非常重要的参数,它对磨粒的磨损有着直接的影响。ts对应于砂带从点A到运动到B(如图1所示)。ts可以用下面的公式来表示:
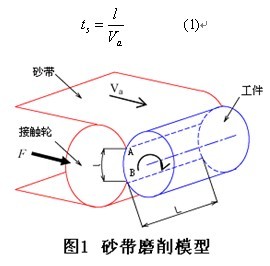
2 工艺试验研究
2.1 实验材料的选用
实验材料选用304不锈钢(国际为0Cr18Ni9),规格为ф35mm×400mm其化学成分如表1所示。
表1 304不锈钢的化学成分(wt%)
2.2实验装置
实验装置由外圆砂带磨床实验机、电子称、表面粗糙度仪、扫描电子显微镜(SEM)等。
实验在重庆市材料表面精密加工及成套装备工程技术研究中心外圆砂带磨削试验机床上进行,同时配备相应的变频器对主动轮进行矢量变频调速实现无级调速。
采用精度为0.1g的电子称来测量工件质量。用秒表记录磨削时间,然后可以算出材料去除率。
表面粗糙度的测定采用针描法,使用北京时代之峰科技有限公司制造的糙度仪TR200,测定的粗糙度参数为Ra。当砂带磨削实验完成后,在扫描电子显微镜上分析砂带表面的微观形貌特征。
2.3实验方案
该实验采用顺磨方式,所采用的实验方案见表2。
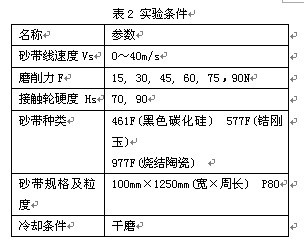
3实验结果分析
3.1材料去除率的影响因素研究
材料去除率,即砂带单位时间去除被加工材料的体积(质量),为了体现砂带宽度影响,一般多采用标准材料切除率,即单位宽度砂带在单位时间内的材料切除体积。在实际测量中采用的标准材料切除率计算公式为
(2)
式中——磨削前后的试件的质量差(g);
——磨削时间(s);
B——砂带宽度(mm)。
3.1.1砂带线速度对材料去除率的影响
图2为磨削压力为40N时,不同的砂带线速度与标准材料去除率的关系。由图可以看出,在一定范围内,标准材料去除率
随砂带线速度Vs增加而增加,但当Vs增加到一定限度时,出现降低。不同磨料砂带对应较好的磨削效果均存在最佳的线速度值,黑色碳化硅磨料砂带线速度约为24m/s,锆刚玉及陶瓷磨料约为33m/s时,材料去除率达到最大值。
从图中曲线变化规律分析可以认为,前期材料切除率增加的主要原因是砂带线速度增加使单位时间内参与切削的磨粒数量
增加,并且由于高速条件下的钝化磨粒也能产生磨屑,所以材料切除率增加;后期材料切除率减小是因为不断增加的磨削速度使弹性砂带上的磨粒受工件表面的反冲击频率增大,弹性砂带退让也增大,引起了砂带磨粒切刃实际切入深度减小。因此,当以上两种因素的影响处于相对平衡时的材料切除率将达到最大值,随后砂带线速度进一步增加砂带实际切削深度和有效切削磨粒数反而减小,最终导致材料切除率下降。
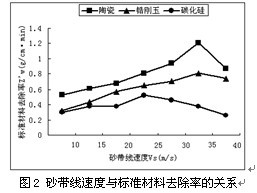
3.1.2 磨削力对材料去除率的影响
图3为砂带线速度为20m/s时,不同磨削力与标准材料去除率的关系。由图可以看出,标准材料去除率随磨削力几乎呈线性增长.这是因为随着磨削力的增加,单位时间内,参与磨削的单颗磨粒平均载荷增加,切入工件更深,材料去除更多。但磨削力并不是越大越好,压力太大,机床振动加剧,磨粒破碎加快、脱落严重,甚至整个砂带断裂,砂带切削能力反而下降[3],材料去除率减小。另外,压力增大,磨削温度升高,工件易烧伤。因此,为了得到较高的材料去除率又不烧伤工件,磨削压力应保持一个适当值。
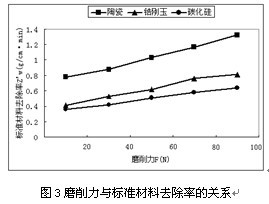
3.1.3 磨料种类对材料去除率的影响
不同种类磨粒在微观结构、抗破碎性、磨损机理方面往往表现出极大的差异,因此对材料的切除率也呈现出很大不同.由图2和3可以看出,陶瓷磨料去除能力明显优于碳化硅。这与磨料本身的特性密切相关,陶瓷磨料韧性好、自锐性好,其特有的微晶结构一般会使磨粒呈现微观破碎。首先微小晶粒峰顶开始形成增大的小平面,其次当小平而增大到一定程度,钝化的晶粒开始破碎脱落,小平而消失并露出次级微小晶粒,也就是说磨粒与材料表层反复摩擦促使其上钝化的晶粒层能及时地断裂脱落并露出新晶粒层,即不断地产生锋利的微切削刃,所以砂带具有很强的自我锐化作用和较高的材料切除率。而碳化硅磨料自锐性差,逐渐磨钝成一个个小平面,主要起抛光作用[8],材料去除能力下降,因此,磨料的种类对材料的去除率影响很大。
3.2表面粗糙度的影响因素研究
磨削加工一般作为机械零件的终加工工序,其主要目的是保证零件的表面粗糙度和形状精度要求.磨削表面的创成过程是磨粒与工件表面材料相互干涉的最终结果.由于磨削过程复杂,影响表面粗糙度的因素众多,磨削过程的物理关系往往很难精确表达[9-10]。
3.2.1磨削时间对表面粗糙度的影响
磨削时间与表面粗糙度的关系如图4所示,从图中可以知道,无论是较硬的还是较软的接触轮,表面粗糙度的变化都分为两个阶段:表面粗糙度值快速降低阶段和稳定阶段。从一个阶段变化到另一阶段的时间与理论上的实际接触时间ts相一致。因此,磨削时间对表面粗糙度的影响很大。当tts时,磨粒的磨损使砂带表面形貌标准偏差稳定地减小,磨粒等高性变好,表面粗糙度的大小也趋于稳定。分析还可知道,随着磨削时间的延长,表面粗糙度值的大小与接触轮硬度的关系不大。
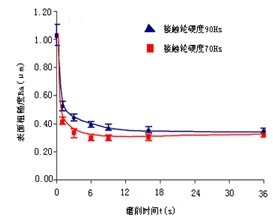
3.2.2磨削压力对粗糙度的影响
磨削压力与表面粗糙度的关系如图5所示,从图中可以知道,表面粗糙度随着磨削压力的增加而降低。当磨削压力大较小时(30N以下),降低的较快;当磨削压力较大时,降低变得缓慢。表面粗糙度值的降低直接与参与磨削的磨粒数Ng和磨粒的形状有关。Ng随着磨削压力的增加而增加,然而,磨粒的形状一方面与接触压力有关,另一方面与磨削时间有关。当磨削压力大时,磨粒的快速磨损使表面粗糙度降低的缓慢。压力的增大,使振动加剧,磨粒脱离严重,Ng减小。
在较小的磨削压力下,磨削时间长一点的比磨削时间短的表面粗糙度要好。这是因为在较小的磨削压力下,磨粒的磨损率较小,并且能保持较长时间的切削性,磨削时间长可以对表面多次磨削,使表面粗糙度值降低。然而,在大的磨削压力下,表面粗糙度的大小与磨削时间的关系不大。
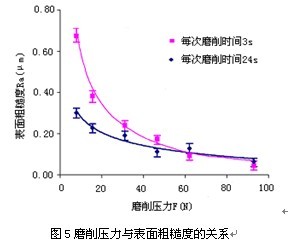
3.3 砂带磨损研究
砂带磨损与磨削效率、加工精度、表面质量和生产成本等密切相关,因此砂带磨损机理也受到了国内外研究人员的广泛关注[11]。
3.3.1磨粒的磨损机理模型
因为磨粒的形状不规则,并且是随机的分布在砂带上,使得磨粒的磨损机理非常复杂[12]。但是,还是可以通过如图6的理论模型对磨粒的磨损做一些定性分析。
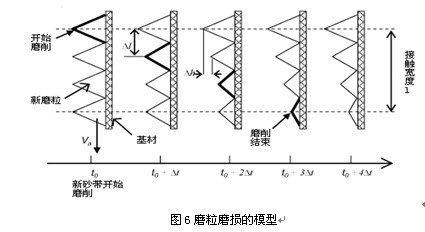
为了研究方便做了如下假设:
①磨粒是椎体;②在很小的磨削时间内,对应磨粒的高度降低;③在时间里,砂带移动距离为。
砂带以恒定的速度Va运动,3是磨粒和工件的实际接触时间,即对应于ts。在3后,与工件接触的磨粒的磨损保持不变,因为总有新的磨粒替代旧磨粒参与磨削。图7描述了磨粒的磨损的过程。如果磨削时间小于ts (如图t1),磨粒磨损程度取决于磨削时间。但是,如果磨削时间大于ts (如图t2),磨损达到最大,不再随磨削时间的变化而变化。
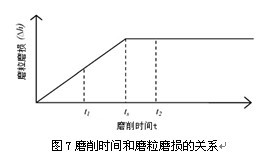
3.3.2砂带磨损表面形貌研究
磨料的微结构和使用条件对砂带磨粒的具体磨损形式和演变过程影响很大。为了提高砂带使用寿命和增加材料切除率,从微观角度来研究不同种类磨料的磨粒磨损形式,进而分析砂带磨损的变化规律[13]。
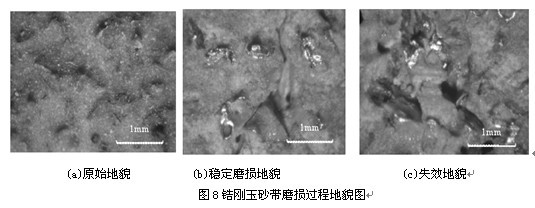
图8(a)是砂带原始的地貌形状,可以看出磨粒间的间隙比较大,磨削刃锋利,而且出露高度很大,这种结构保证了磨削过程中砂带不易堵塞。
图8(b)是稳定磨损时砂带的地貌形状,磨粒出现脱落,但不是很严重。此时磨粒的粘附现象很明显,观察粘附的不锈钢基本上都是细长的磨屑,这些磨屑 在外力的作用下很容易整个脱落下来。其来源是因为错刚玉磨粒切削刃锋利,出露高度大,磨削时很容易切下细长的磨屑,此时磨粒磨损主要以摩擦磨损和粘附磨损为主。
随着磨削的进行,磨粒出现严重的脱落,磨粒出现不断增大的磨钝小平面,磨粒失去切削能力,砂带失效。如图8(c)所示。
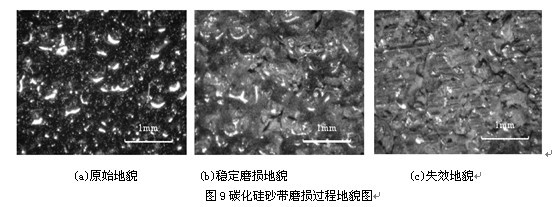
图9(a)是碳化硅砂带的原始地貌。从图中可以看出其磨粒出露高度比锆刚玉砂带小很多,而且磨粒分布也比较紧密,这种结构致使砂带比较容易发生堵塞现象。
图9(b)是砂带稳定磨损时的地貌照片,此时砂带以摩擦磨损为主,但是此时砂带已经出现堵塞现象,而且磨粒也开始出现脱落现象。
图9(c)是磨损后期砂带的地貌图,此时砂带磨损以堵塞和脱落为主,砂带失效。
通过以上对比分析可以看出,锆刚玉砂带的磨损过程比较复杂,在磨削初期主要以破碎磨损为主,在稳定磨损阶段,以摩擦磨损和粘附磨损为主,在磨削后期主要以脱落磨损为主。而碳化硅砂带的磨损过程则比较稳定,在磨削初期和稳定磨损阶段都以摩擦磨损为主,在磨削后期则以脱落和堵塞为主。
4 结论
(1)砂带线速度及法向磨削压力对标准材料去除率有较大的影响.标准材料去除率随线速度的增大而增加,但超过一个临界值后速度继续增加,材料去除率则下降。标准材料去除率随磨削压力呈线性增长,但磨削压力太大,砂带磨损严重,导致材料去除率下降. 陶瓷磨料具有很强的自我锐化作用和较高的材料去除率,因此是加工304不锈钢的理想磨料。
(2)磨粒和加工表面的实际接触时间ts对表面粗糙度Ra和砂带磨损有很大的影响。当tts时,表面粗糙度和砂带磨损趋于稳定。
(3)在磨削时间大于ts后,表面粗糙度值的大小与接触轮硬度的关系不大。在保证砂带磨损不是很严重的情况下,可以尽量使磨削压力大一点,以提高材料去除率和减小表面粗糙度。
(4)锆刚玉磨料的磨损过程比较复杂,前期以破碎磨损为主,稳定和后期则以摩擦磨损为主。碳化硅砂带磨粒分布也比较紧密,砂带更易堵塞,磨损过程则比较稳定,在磨削初期和稳定磨损阶段都以摩擦磨损为主。
参考文献:
[1] 熊家强,谢刚,唐广波.304不锈钢热变形过程奥氏体动态再结晶及流变应力研究[J].云南冶金,2008,37(5):37-42.
[2] Gajendra P S, Alphonsa J, Barhai P K. Effect of surface roughness on the properties of the formed on AISI 304 stainless steel after plasma nitriding[J]. Surface & Coatings Technology, 2006, 200:5807-5811
[3]王德泉,陈艳.砂轮特性与磨削加工[M].北京:中国标准出版社,2001:219-220.
[4] 李宝膺,华丽,石占先.不锈钢抛光工艺与磨具选择[J].金刚石与
磨料磨具工程,2007(4):72-74.
[5] Minori N, Mamoru K. Experimental study on grinding fluids for abrasive belt grinding of stainless steel[J]. Journal of Japan Society of Lubrication Engineers,1985,6(5):157-162.
[6] 黄云,黄智.现代砂带磨削技术及工程应用[M].重庆:重庆大学出版社,2009:8-9.
[7] 黄云,黄智. 砂带磨削的发展及关键技术[J]. 中国机械工程,2007, 18(18):2263-2267.
[8]王维朗, 潘复生, 陈延军等.不锈钢材料砂带磨削试验[J].重庆大学学报(自然科学版),2006,29(10):91-95.
[9] Bigerelle M, Najjar D, Iost A. Relevance of roughness parameters for designing and modeling machined surface[J].Journal of Materials Science,2003,38(11):2525-2536.
[10] 修世超, 李长河, 蔡光起. 磨削加工表面粗糙度理论模型修正方法[J]. 东北大学学报(自然科学版),2005,26(8):770-772.
[11] Jourani A, Dursapt M, Hamdi H, et al. Effect of the belt grinding on the surface text: Modeling of the contact and abrasive wear[J]. Wear, 2005, 259:1137-1143
[12] Mezghani S, Mansori M, Sura E. Wear mechanism maps for the belt finishing of steel and cast iron[J]. Wear, 2009, 267:132-144.
[13] Deuis R L, Subramanian C, Yellup J M. Abrasive wear of aluminium composites—a review[J].Wear,1996,201:132-144.
黄云 黄智 杨俊峰杨春强