在半导体相关产业和航空宇宙相关产业所用的净化管内表面,为防止污染物的粘附和滞留,而要求高精度的内表面。如沿用目前采用的磁性粒子内表面研磨法,这对壁厚<5mm的圆管内表面的精密加工是有效的,但由于工件的壁厚如为10mm左右,不但需要花费很长时间来加工,甚至会使加工失败,目前采用的磁性粒子利用方法加工,无法加工壁厚在10-30mm间的圆管内表面,圆管内表面的加工作为长期洗净工程无疑将成为另一话题。
本文为适应社会需求,开发出借助于磁力作用的高效、高精内表面研磨法,提出是用一种磁性加工夹具借助磁力的新思路,这将比用老的磁性粒子利用法得到高几十倍的磁力,能够实现对厚壁圆管内表面的镜面加工。
用磁性加工夹具加工法,是将加工夹具,利用构成永久磁铁端面的磁力特性,将磁性粒子在加工夹具端面受磁力吸附,并通过磁性粒子作媒介,提出一种新的“磁性粒子与研磨糊膏并用的磁性加工夹具的利用法”,这种加工法显著延长了工具寿命,并能具有可自由选择磁性粒子与研磨材种类和粒径的优点。
通过这种方法同样也能对10mm厚的厚板园表面进行高效高精的加工。
2、磁性粒子利用法与磁性加工夹具利用法的特性比较
图1(a)为原来的磁性粒子利用法,图1(b)为新提出的磁性加工夹具利用法的示意图。如图1(a)所示,磁性粒子利用法是依靠磁力来连接磁性粒子群,沿着工件表面呈现挠性动作,它虽能有维持原有形状精度和表面平滑的特点,但磁性粒子群体的磁化率比仅为2~3,与钢铁那个值比低得多,为此对加工工件壁厚大于5mm者,显得力不从心,无法胜任加工。
另一方面,磁性加工夹具利用法,是将磁铁与磁性材U形块构成一体,磁性材本身具有高磁化率,能产生高的磁力,如图1(b)所示,用永久磁铁所构成的N-S极作成对型磁性加工夹具时,能构成封闭磁力回路,在这封闭磁力回路中,由于磁抗极小化,加工夹具涉及到工件表面的磁力(加工力)能相当的高。
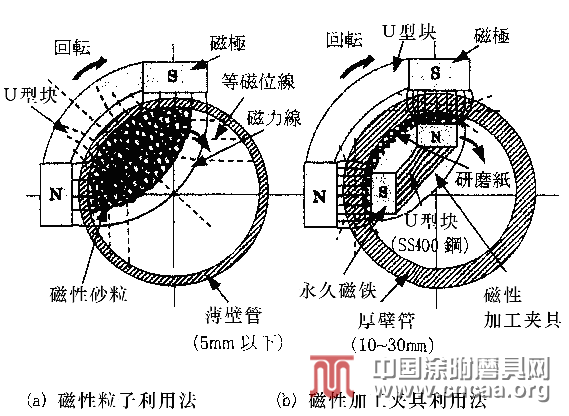

图3为实验条件及测试结果,如图作为磁性粒子用平均粒径为510μm的电解铁粉,其磁力为0.4N,用SS400钢材型磁性加工夹具时为0.7N,相比之下,SS400钢材型磁性加工夹具的磁力增大,效果不怎么明显,当如用单一磁铁内藏型磁性加工夹具时,磁力效果明显增大,再进一步用N·S极相对型磁性加工夹具时,由于能构成封闭磁回路,磁抗减小,比单一磁铁内藏型能够得出磁力增大的效果,用N·S极相对型磁性加工夹具时,其磁力比用电解铁粉时的磁力约能提高80倍。
然而,论及研磨加工机理,研磨压力应是首要因素,于是磁性粒子及各种磁性加工夹具的磁力(图3)相对不同的工具面积可求得研磨压力。图4所示为磁性粒子与各种磁性加工夹具研磨压力的比较。
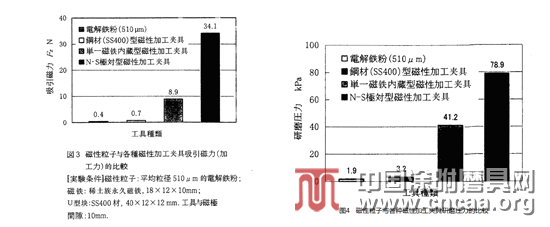
3、“磁性粒子与研磨材糊膏并用的新的磁性加工夹具的利用法”的加工原理
如图5所示,N·S相对型磁性加工夹具与圆管上外设的磁极间构成磁力回路,在与工件间发生具有高磁吸力(加工力)的相对运动力,磁性加工夹具随着磁极回转运动而回转,在圆管内面与其间产生相对运动,在磁性加工夹具的永久磁铁端面,吸附着磁性粒子所介入的研磨糊膏中的砂粒加工作用,实现内管内面的精密加工。另外,如再施于圆管轴向运动的话,即能实现圆管内面的全方位加工。
通过此法,促进了研磨材的新陈代谢与排屑作用,并具有能够对磁性粒子与研磨材粒径自由选择的优点,由此高效、高精内面精密加工期待能够实现
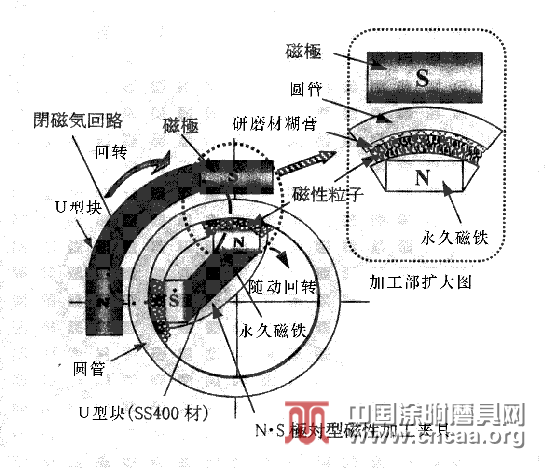
如图6所示,新制作的磁极回转单元装置于车床滑台上,这个单元由4个铁氧体磁铁(50*35*26mm)成S-N-S-N排列,将此通过U型块连接与N·S相对型磁性加工夹具形成封闭磁回路。普通车床滑台上装上加工单元,在圆管方向90mm区间作往返的送进运动来加工,完成圆管内面90mm全宽范围内的加工。
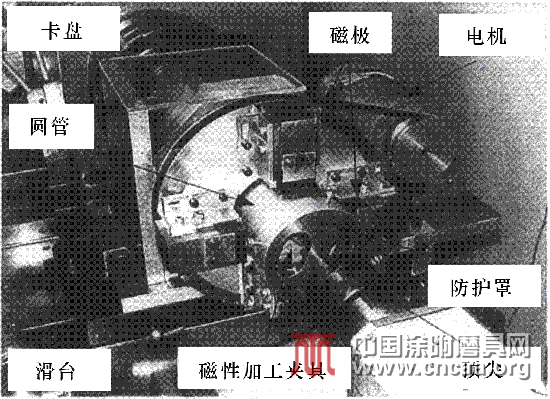
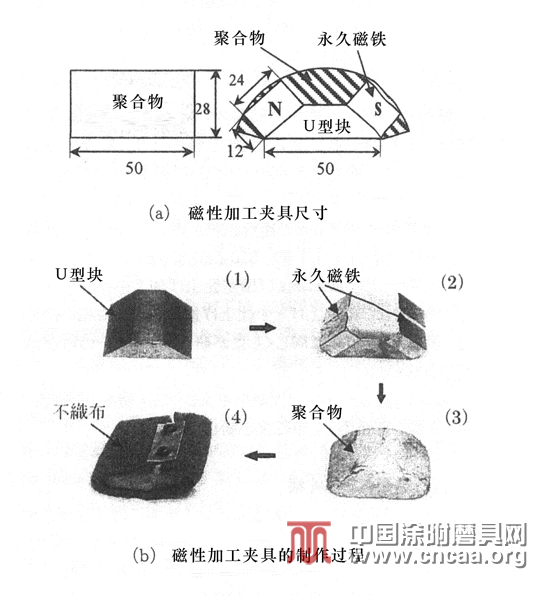
表1为研磨实验条件。
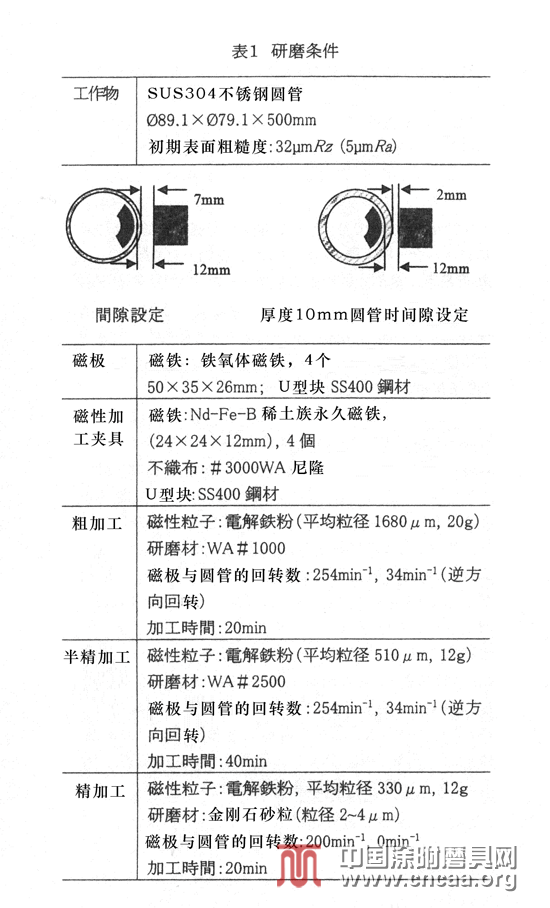
一般热加工出来的厚壁SUS304不锈钢管,原加工面有氧化膜,表面粗糙度在30-40μmRZ的较大值范围内,为此加工需分三阶段进行,粗加工用平均粒径1680μm的电解铁粉,然后用电解铁粉平均粒径较小的510μm和330μm的电解铁粉来进行半精加工及精密加工。表1所示粗加工及半精加工磁极转数与圆管的回转数相同,所变化的仅是研磨材糊膏的粒度。
5、实验结果与考察
从实验结果观察,在磁性加工夹具端面,受磁力吸着的磁性粒子(电解铁粉)有力地吸附在加工夹具端面,本法的实验得到了确认。
加工前后的磁性加工夹具的状态与圆管内面外观的照片示于图8。
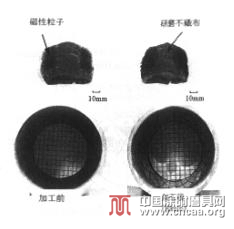
图9为加工机理的模型图。图中显示在圆管内部装置的磁性加工夹具,因在圆管外侧设置磁极受有高的磁性吸力Fm(加工力)和相对运动力,因而在磁性加工夹具的永久磁铁端面上被磁力吸附着的磁性粒子参与加工,本实验在磁性加工夹具的外周全面地贴附研磨不织布,其如图9所示。
磁性粒子(电解铁粉)由于加工夹具的永久磁铁受磁力吸引,在不织布的间隙处可目测到隆起现象,由此明确了磁性粒子停留在研磨不织布上并保持在加工夹具端面上的加工作用。
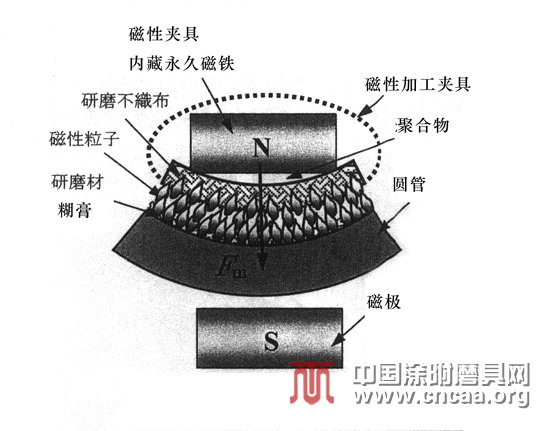
图10表示的是表面粗糙度与加工量、时间变化的结果。
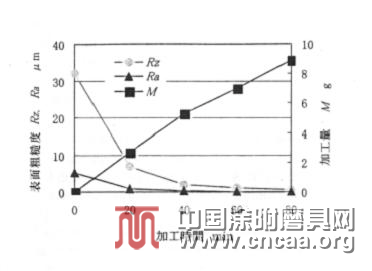
本加工法,圆管轴向90mm范围内,表面粗糙度能提高至0.49μmRZ(0.05μmRa)。
图11为用线切割切取试片的表面照片和表面粗糙度分布图,描述的是在白纸上条格花纹照片的观察结果,条格花纹得到充分反射,这证明本加工法对壁厚10mm的厚壁不锈钢管内面的镜面加工是适用的。
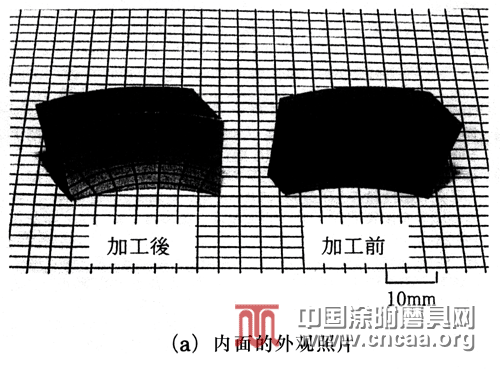
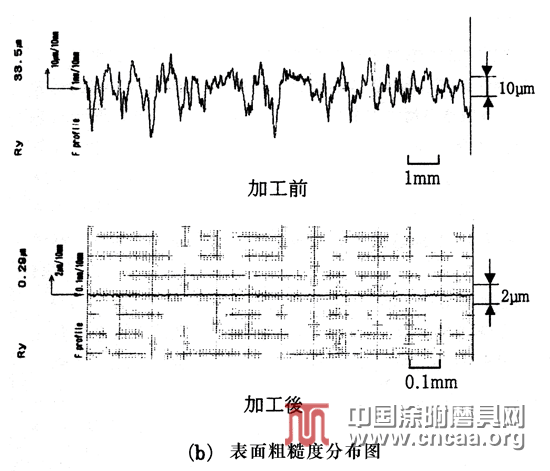
图11(a)是线切割取出观察片描述在白纸上条格花纹的照片,经观察加工前的厚管内面条格花纹全部无反射,加工后的内面条格花纹明显得到反射。
图11(b)为表面粗糙度分布图,加工前的表面粗糙度从33.5μmRZ提高到0.29μmRZ,并图示的表面粗糙度所表示的最大表面粗糙度Ry相当于新标准Rz。
试验用圆管是经热加工的SUS304不锈钢,因热加工圆管内面有氧化膜,为了弄清本研究课题“磁性粒子与研磨材糊膏并用的磁性加工夹具利用法”能否除去氧化膜以及观察表面生成的切割刃交叉轨迹的存在,通过线切割切出加工部与未加工部二段,用扫描电子显微镜观察。
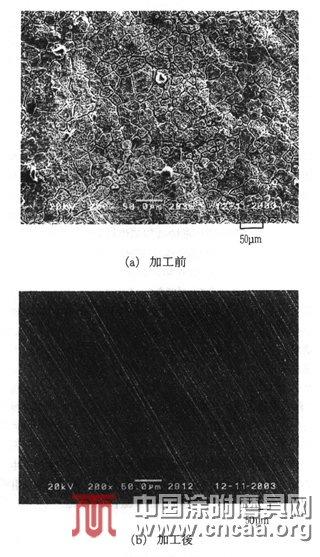
另外,原来的磁性粒子利用法,采用同样加工条件,即使用粒径1680μm的电解铁粉,加工结果证明也几乎不可能成功。
6、结论
本研究“磁性粒子与研磨材糊膏并用的磁性加工夹具利用法”适用于壁厚>10mm的厚壁不锈钢管内面的精密加工,验证了观察性,得到如下几点结论:
⑴利用磁性加工夹具比原来磁性粒子利用法,设置间隙10mm时,N、S相对型磁性加工夹具法作用的磁力(加工力)比用磁性粒子利用法加工时大出80倍,完全能实现壁厚>10mm的厚壁管的内面精加工。
⑵普通车床上装上专用加工的装置与磁性夹具,用本法对厚壁不锈钢管内表面的精加工结果能达到圆管内表面粗糙度由32μmRZ提高至0.49μmRZ。
⑶用扫描电子显微镜观察,由热加工形成的厚壁不锈钢圆管加工面存有的氧化膜能彻底去除,并明确了砂粒切削刃的微小研削作用,所形成的加工面机理。
⑷本加工法对厚壁圆管内面的镜面加工有效,具有一定的工业实用性。
本文原载于日本“バリ取リ加工,研摩布纸加工技术专门委员会”2011年会报
译者简介:吕振安,男,高级工程师,原新乡机床厂总师办主任,日本研磨布纸加工技术研究会特别会员