典型案例:航空发动机叶片磨削、汽轮机叶片磨削、螺旋桨叶片磨削、整体涡轮盘抛磨、高档异型水槽高效磨边加工、钛合金管抛磨
高精度、数字化磨削加工设备的特点:
1.由于加工对是复杂曲面,采用多轴联动数控加工技术;
2.对磨削压力比较高,采用能够保持恒压的磨头机构;对于叶片抛磨,在使用六轴数控加工技术的基础上增加了法向压力控制轴;
3.对机床本身的精度要求高;
4.在线检测技术与数控加工技术相结合;
5. 根据加工零件尺寸,机床体积大小不同。
一、高档异型水槽高效磨边加工
通过先进数控技术结合砂带磨削技术,解决了高档异型水槽自动化磨边的技术难题,填补了国内相关技术领域空白.
该装备2006年在广东FRANKE(瑞士)公司已经加工10多万套星盆产品,顺利通过原厂检验并返销国外3万套,为该公司节省进口同类欧洲加工设备约12万欧元。
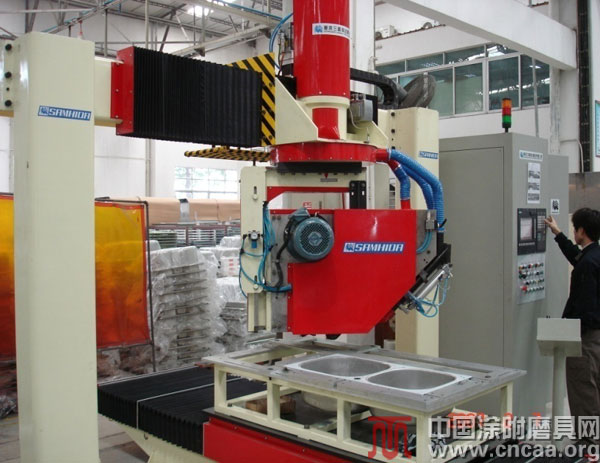
锆合金包壳管的作用是包容并封装燃料芯块,避免其受冷却液的腐蚀与机械冲腐、包容裂变产物以及燃料元件提供结构支撑等。
为了使包壳管达到使用要求,必须要经过包括壁厚修磨在内等十余道工序的加工处理。
均匀壁厚直接影响到包壳管的冷加工和真空退火质量,Zr-4 锆合金管材在进入包壳管生产厂之前必须要对其内外表面做相应的处理以除去内表面的挤压缺陷和油污,外表面的致密氧化膜、棱状条纹、沟痕缺陷以及坑状瑕疵等宏观缺陷,并达到规定的管材壁厚和表面光洁度。
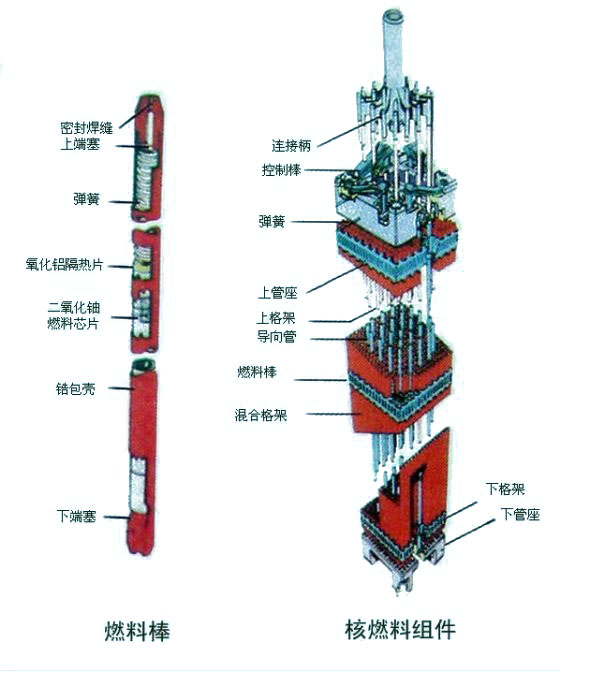
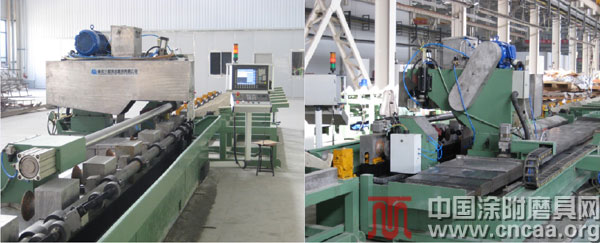
核反应堆锆合金管坯壁厚砂带自动修磨技术集成了砂带磨削工艺、超声波测厚及数控加工等数项关键核心技术
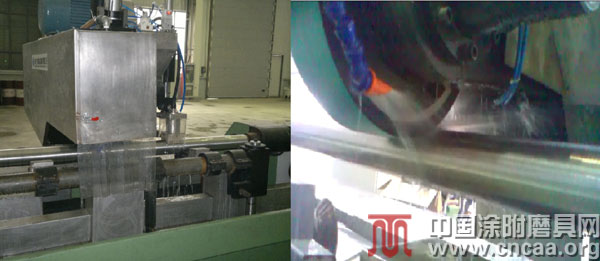
随着科学技术的进步,我国对能源、运载、国防等领域重大工程关键结构零件的质量提出了更高要求,其型面制造效率、加工精度和表面粗糙度对整个能源与动力转换装置的性能和效率都有着至关重要的影响。
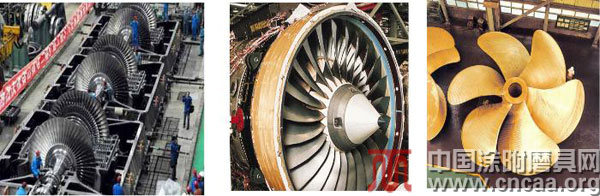
汽轮机 航空发动机 螺旋桨推动器
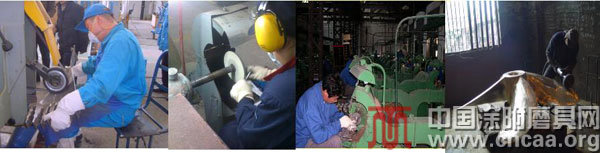
叶片磨削加工现状
针对船用螺旋桨型面常采用五轴联动数控铣削加工,单因铣削加工的表面质量较差,使得其对船用螺旋桨推进效率与疲劳强度影响较大,加之船用螺旋桨存在铣削加工产生的变形,船用螺旋桨表面必须磨削或抛光加工。
目前我国对螺旋桨叶片的抛光主要为人工抛磨,虽然能实现复杂曲面的打磨与抛光,但叶片表面的质量由人员的熟练程度决定,因而无法做到对工件尺寸精度的有效管控,导致加工精度较差、型面的质量难以保证。

螺旋桨叶片
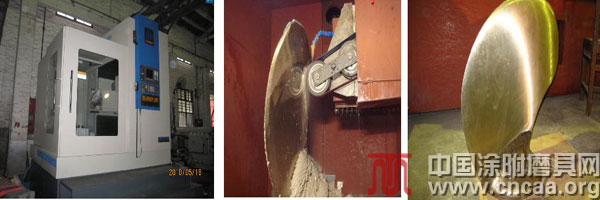
四轴联动螺旋桨砂带磨床 叶片磨削现场 调距桨叶片磨抛效果
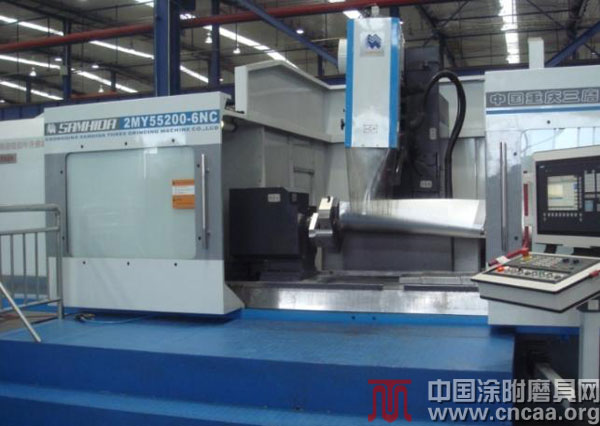
磨削前后效果对比
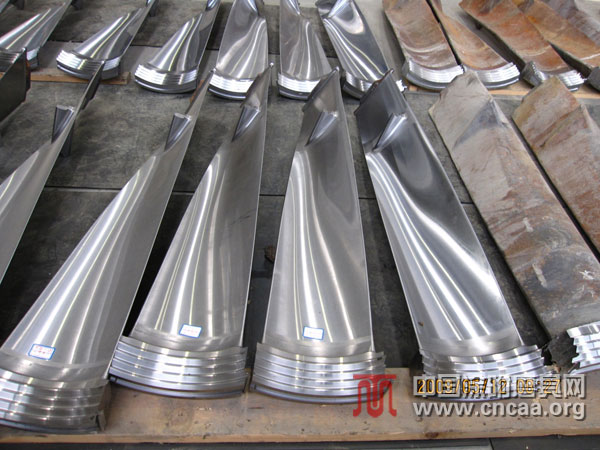
型面精度<0.05mm
Ra<0.1μm
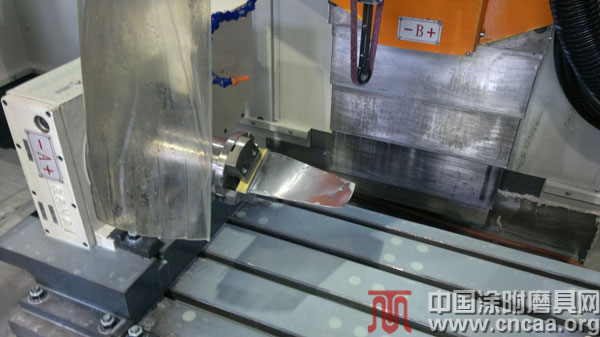
六、航发叶片七轴六联动高效精密砂带磨削
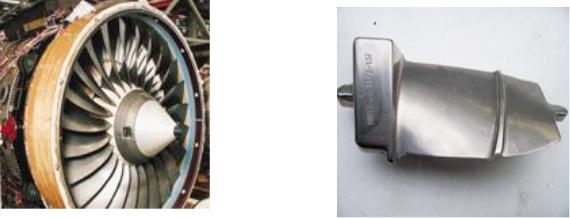
叶片通常由具有一定强度的难加工材料制成,如采用高温合金、镍基合金、钛合金等。因叶片材料含有昂贵的高温合金元素,加工性能比较差,且叶片型面是复杂空间自由曲面,因此加工难度大。
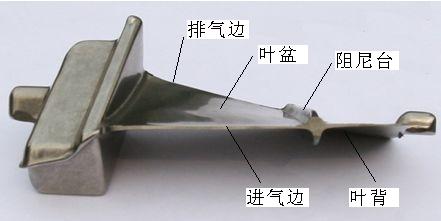
为满足发动机高性能、工作安全性、可靠性以及寿命的要求,叶片必须具有精确的截面形状与尺寸、严格的表面完整性,同时允许叶片有一定角度的扭转变形。截面形状与尺寸对发动机的效率、推力以及空气的流向都有重要影响。如果叶身型面与进排气边的截面形状与尺寸精度(进排气边缘与叶身转接的真实R弧形精度)达不到设计要求,则可能导致航空发动机出现紊流、气喘、怠速不稳、失速等现象,严重时可危及到飞行安全。
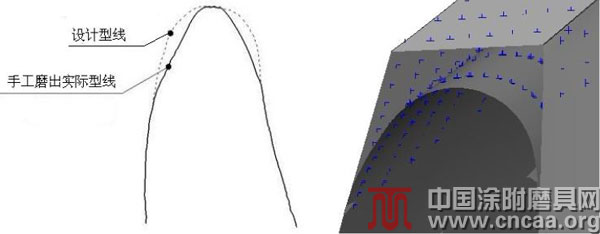
国内航空发动机精锻叶身无余量叶片边缘的加工则是采用普通铣床切除毛坯上锻造飞边,而后采用手工打磨叶片的进出气边、并通过投影的方法肉眼观察打磨质量。由于航空发动机叶片边缘最小厚度不超过1mm,其截面曲线形状为圆弧或者其它样条曲线,采用手工打磨进出气边容易出现弦长超差、方头、截面曲面形状及位置超差、不符合真实R型面要求等问题,导致叶片废品率较高、产品一致性差等问题,严重制约了叶片质量。
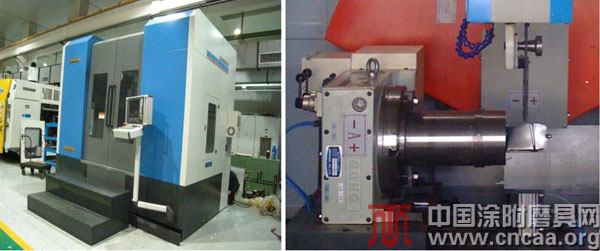
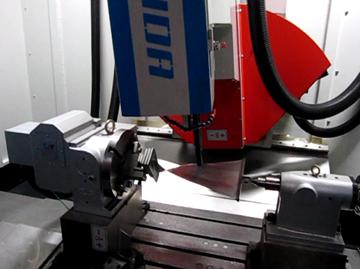
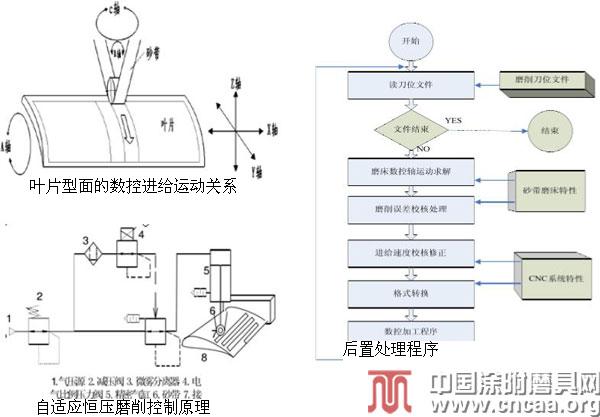
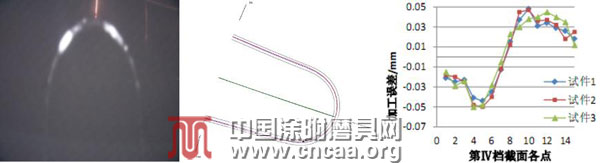
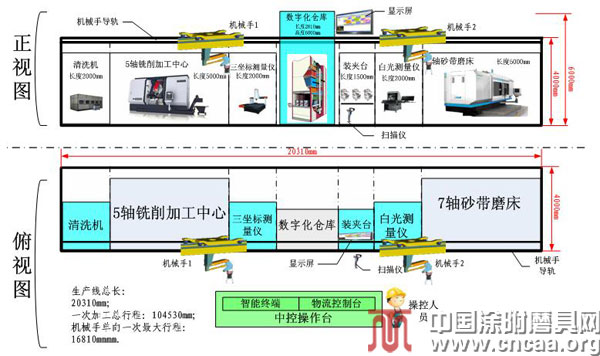
砂带及磨料的选用
国外研发的精细砂带形式和种类较多,其中最具代表性的是美国3M公司运用其独创的微晶复制技术所开发出来的金字塔堆积磨料砂带。
3M金字塔堆积磨料砂带是由外形规则整齐排列的四棱锥磨粒构成,每个大磨粒都包含了多层的研磨矿砂。
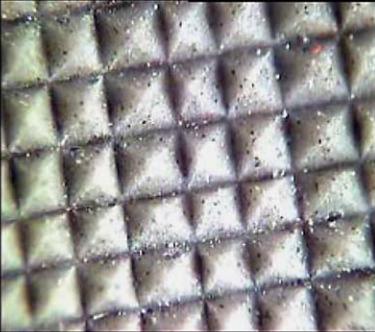
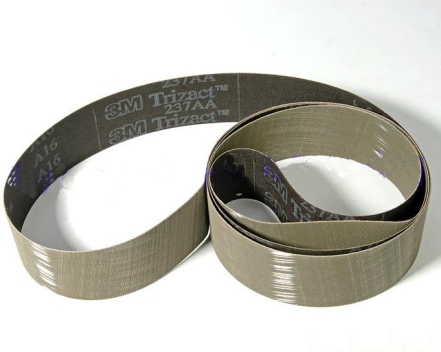
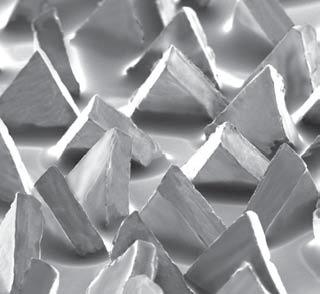
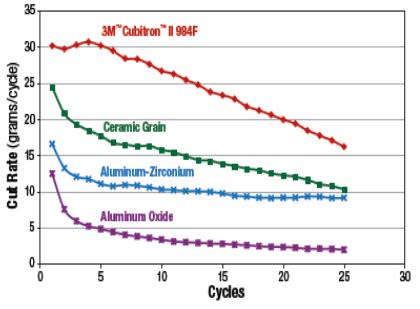
使用寿命是传统陶瓷颗粒砂带的四倍。
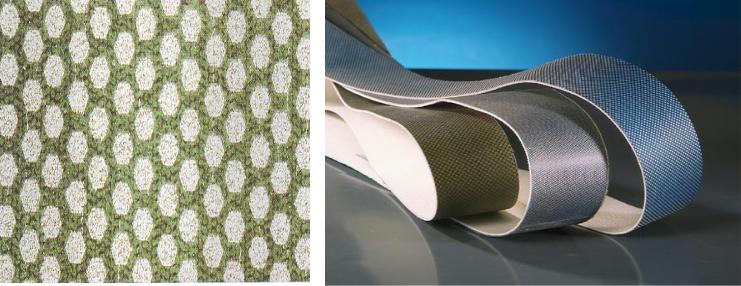
超硬磨料砂带