(1.吉林工程技术师范学院,吉林长春130052;2.长春理工大学,吉林长春130022)
摘要:本文以聚醚和多异氰酸酯为原料,用预聚体法合成了聚氨酯胶粘剂用于汽车顶棚胶。介绍了聚氨酯胶粘剂的合成工艺,确定了反应物的配比,并对反应用催化剂,反应温度,反应时间等条件进行了讨论得出最佳工艺。结果表明,采用聚醚混合物与异氰酸酯的配比为4.5:1,催化剂用三乙烯二胺和辛酸亚锡的混合催化剂且用量为0.15%,温度为80±5℃的条件下,反应4.5h得到的胶粘剂具有良好的性能。。
关键词:预聚体;聚氨酯胶粘剂;湿固化;单组分
聚氨酯(PU)胶粘剂是分子链中含有氨酯基(-NHCOO-)或异氰酸酯基(-NCO)类的胶黏剂。由于其具有高的活性和强极性,对多种极性材料有良好的粘附性。汽车顶棚一般用织物复合聚氨酯泡沫或聚氯乙烯薄膜复合聚氨酯泡沫来做材料,汽车顶棚胶粘剂是用来将软质顶棚材料粘贴到车身顶盖上,使其与顶盖完美的结合,起到隔热隔音的作用,也增添了车内的美观性。汽车用单组分湿固化PU胶大多使用聚醚作原料,增加了胶粘剂的柔软性能,也提高了胶粘剂耐水、耐冲击、耐振动的性能,其在空气中遇水固化的特点又使其在汽车的工业化的大生产中受到重视。为适应汽车工业中自动化生产线的需要,胶粘剂的固化速度必须适中,大约30分钟左右。本文用预聚体法合成的的汽车用顶棚胶固化时间适中,而且在固化过程中不会产生气泡和裂纹,稳定性很好,粘接性能优异,完全适合工厂中的生产工艺要求[1]。
1·实验部分
1.1 原料
多亚甲基多苯基多异氰酸酯(PAPI)44V20,德国,工业品;聚醚220,广州辉煌化工科技有限公司,工业品;辛酸亚锡,常州石油化工厂;三乙烯二胺,常州石油化工厂,工业品。
1.2 所用仪器
500ml三颈磨口烧瓶,2XZ-1型旋片真空泵,DM型直热电热套,JB50-D型增力电动搅拌机(100-1300转/分)。
1.3 实验流程
首先将聚醚220加入到三口烧瓶中,升温到120℃,在真空下脱水3h,然后冷却到60℃,在N2保护下加多异氰酸酯进行反应1h。完成后加入混合催化剂在80士5℃进行反应15-20min。然后结束反应,趁热倒出产物,于容器中密封包装。
2·结果与讨论
2.1 异氰酸酯指数R(NCO/OH的摩尔比)的确定
反应物中聚醚混合物和异氰酸酯的比例是关系到整个胶粘剂好坏的关键,而且要考虑到胶粘剂的粘度,固化速度等因素.一般R值越高,密度、粘接强度,等与硬段有关的性能值提高。但是如果R值太高,则因为固化时没有那么多水分提供给预聚体固化,则胶粘剂的固化时间缓慢,即使可喷洒水雾或者添加稍多催化剂的方法促进固化,也会因为产生的二氧化碳气体有不及逸出使胶层发泡,降低粘接强度[2]。
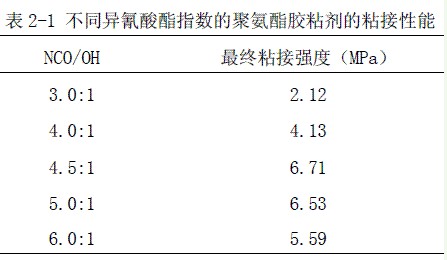
从表2-1实验结果可看到,随异氰酸酯指数增加,聚氨酯胶粘剂分子中刚性基团增加,表中数据显示在异氰酸酯指数为4.5:1时胶的固化速度适当且最终粘接强度最高。
2.2 温度的确定
聚醚的脱水温度为110-120℃,同时抽真空和搅拌。这样的温度己足以使体系内的水分气化,抽真空及搅拌主要是帮助脱除水分,因为聚醚粘度较大。脱水这一步很关键,如果水没除干净,会改变反应体系异氰酸酯指数,甚至发生交联反应。而在反应后期温度也不能太高,否则会引起凝胶反应。在加异氰酸酯后分别设置60℃、80℃、100℃[3]这三个温度进行试验。
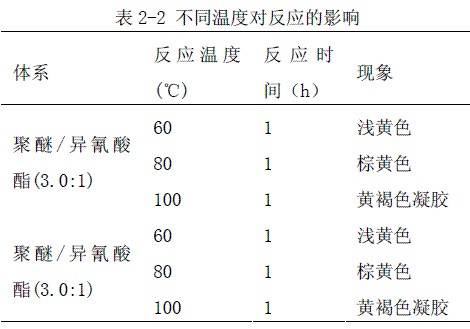
由表可知,在60℃时,因温度低,体系粘度大,反应不完全,以致影响到聚氨酯胶粘剂质量:在100℃时,因温度太高,体系粘度急剧增大,凝胶效应凸显出来,可见,控制温度为80±5℃是合适的[4]。
2.3 催化剂种类及用量的确定
应用于聚氨酯胶粘剂工业上的催化剂种类繁多,常用的只有叔胺类及有机锡类。实验中我们选用来源广泛的三乙烯二胺和辛酸亚锡。加催化剂的目的主要是提高反应时间,加速其固化速率,即提高-NCO基团与H2O的反应速率。因此催化剂在形成预聚体后,温度仍维持在80士5℃加入。为了考察不同催化剂对固化速率的影响,我们将MDI/PPG(NCO/OH=3.0:1)体系添加不同催化剂第一组加辛酸亚锡;第二组加三乙烯二胺;第三组加三乙烯二胺和辛酸亚锡的混合催化剂[5]。
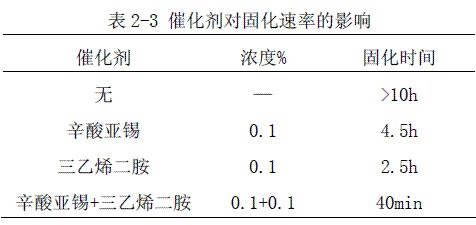
从表2-3可知,三乙烯二胺的固化时间比辛酸亚锡要短,说明三乙烯二胺对-NCO/H20的反应的催化效果比辛酸亚锡好,而由于协同效应,使用混合催化剂的效果远高于单一催化剂的效果。
催化剂的用量的大小决定着反应时间的快慢,太少则没有作用,太多则会使反应速度太快而引起爆聚,所以选取含量0.1-0.25%来进行实验,看哪个含量更适合。
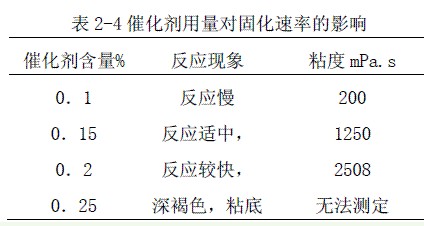
表2-4可知,含量0.15%时反应速度适中,生成的胶粘剂粘度也较好。
3·性能测试
3.1 性质测试
(1)固含量:56.7%;
(2)黏度(室温):560~1550mPa·s,且随温度变化幅度较小;
(3)粘接强度:6.71MPa
(4)贮存期:6个月。
(5)固化时间:35-45min
3.2 红外光谱检测
在红外光谱下检测产物得其红外光谱图如下:
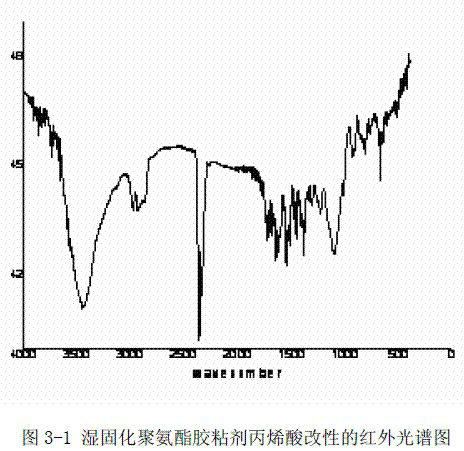
由样品的红外吸收光谱图3-1可以看出,在3460cm有典型的NH基伸缩振动峰,在1540cm有NH基的弯曲振动峰。2350cm峰和1440-1200cm.吸收峰证明有-CO基团和-COO基团的存在,因此产物为含-NH-COO-基的高分子,而2870cm处的吸收峰则表明分子链中含-NCO基团。另外一些吸收峰的归属分别为3560cm及36100cm是-CH3的伸缩振动峰;1640cm和1550cm是-CH3的面内弯曲振动;1798cm是苯环氨酯基NH的变形振动;1182cm是OC-O-C的C-O-C键的对称伸缩振动[13]。即含有NH基;-NH-COO-基;-NCO基团;-CH3;苯环氨酯基。
4·影响因素分析
4.1 聚合过程中的凝胶现象
导致凝胶事故的可能原因包括:(1)第一步脱水时水没脱干净;(2)NCO/OH量比过低;(3)反应温度过高或测温系统失效;(4)催化剂的量过多或分散不均匀导致局部反应剧烈;(5)原材料不同批次反应活性差别大;(6)温度过高等。本次实验中的因为控制好了反应条件,在最佳条件下,没有产生凝胶的现象。
4.2 贮存稳定性
湿固化聚氨酯胶粘剂体系中含有游离的NCO基团,所以它极易与环境湿气或含活泼氢的化合物反应,这是造成胶粘剂不稳定的主要因素。另外为了避免原料中某些碱性物质的存在(碱能加速异氰酸酯的所有反应)而导致的凝胶现象,可以在后期加入酸性的缓凝剂,如磷酸或苯甲酞氯以减少凝胶机会,使反应正常进行。此外,操作工艺也是主要的影响因素。端NCO基聚氨酯胶粘剂的稳定性还受贮存容器的密封性、容器壁性质及容器内气体的影响[6]-[8]。
目前我国对聚氨酯胶粘剂中的游离异氰酸酯单体含量的限制越来越严格,制备低VOC(挥发性有机物含量)和低游离异氰酸酯单体开始受到重视。除了注意控制搅拌速率、使反应均匀以外,一般是在丙烯酸改性后采用真空薄膜蒸发工艺,在短暂高温状态下减压闪蒸,故而要在固化速度和贮存性能之间寻找一个平衡点[9]-[10]。
5·结论
合成单组分湿固化汽车顶棚用聚氨酯胶粘剂的最佳合成工艺为:聚醚混合物与异氰酸酯的配比为4.5:1,催化剂用三乙烯二胺和辛酸亚锡的混合催化剂且用量为0.15%,温度为80±5℃的条件下,反应4.5h得到的胶粘剂具有良好的性能,最终粘接强度为6.71MPa,且贮存期6个月。
参考文献
[1]凌爱莲,桑红勋,甄铁,等.湿固化型聚氨酯胶粘剂[J].中国胶粘剂,2002,12(6):26-29.
[2]杨建恩.单组分湿固化聚氨酯胶粘剂建筑密封胶的生产工艺[J].粘接,2002,23(3):4-6.
[3]黄汉东.单组分湿固化聚氨醋密封材料的研制[J].福建建材工业,2002(1):20-22.
[4]李永德,谭上飞.单组分湿固化型聚氨醋密封胶催化剂的研究[J].粘接,2000,21(2):4-6.
[5]李绍雄,刘益军.聚氨酯胶粘剂[M].化学工业出版社,1998.
[6]傅明源,孙酣经.聚氨酯胶粘剂弹性体及其应用[M].化学工业出版社,1999.
[7]刘益军,等.聚氨酯胶粘剂[M].北京:化学工业出版社,1998.
[8]李鑫,徐伟箭.反应型聚氨酯胶粘剂聚氨酯胶粘剂研究进展[J].湖南化工.
[9]宁志强.快速固化汽车顶棚胶的研制[J].化学与粘合,2007,29(3):179-181.
[10]杨足明,杨冬梅,等.汽车用单组分湿固化聚氨醋胶粘剂研究进展[J].中国胶粘剂,2005,14(7):33-36.
[11]李永德,杨颖霞.单组分湿固化聚氨酯胶粘剂[J].中国胶粘剂,2002,12(2):51-55.