1 实验装置设计及实验方法
开式砂带磨削采用成卷的砂带,通过收带轮转动带动砂带作缓慢的移动,砂带由接触轮压向工件实现对工件表面的磨削加工。由于砂带缓慢的移动,磨粒不断投入磨削,磨削效果一致性好[8]。根据砂带磨削实验需要,笔者设计了一台综合砂带磨削装置,将其装夹在车床的横拖板上,并随车床横拖板作纵向和横向进给运动实现砂带磨削(见图1)。
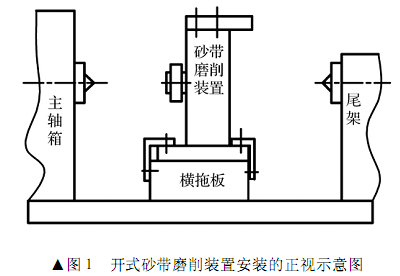
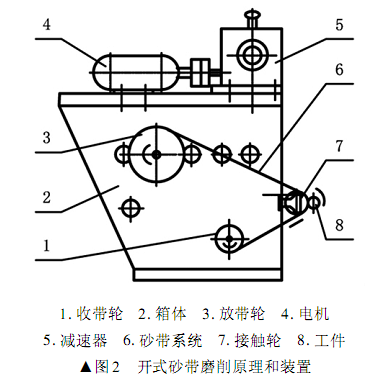
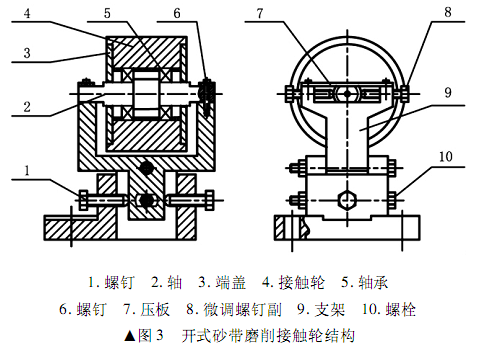
实验条件:工件转速 nw = 1250r/min;砂带转速ns = 2r/min;进给量f = 0.01mm/r;平面橡胶接触轮;工件材料40钢
2 尺寸精度研究与分析
2.1 实验数据
随机抽取四个工件,每个工件在车削完成后,分别在五个截面处从两个方向测量其直径尺寸,算出磨削前最大尺寸误差;之后对工件进行砂带磨削,磨削完成后,同样在五个截面处从两个方向测量其直径尺寸,算出磨削后的最大尺寸误差,实验数据见表1。
实验数据表明,砂带磨削前工件尺寸误差在0.01—0.025 mm,尺寸精度在IT6-IT8范围内;砂带磨削后尺寸误差为0.005-0.017 mm,尺寸精度在IT5-IT7范围内。可见砂带磨削后工件的尺寸精度均可提高1-2级以上。同时从实验数据中可以看出,当车削加工完成后,直接进行砂带磨削提高尺寸精度是有效的。而且砂带磨削对工件前道工序产生的锥度、腰鼓肚现象能起到部分消除的作用。

2.2 影响尺寸精度的因素
(1) 微量进给精度。砂带磨削微量进给精度主要决定于四个因素,一是细长轴刚度弱,磨削时由于磨削力的作用,刚度弱易变形,影响了微量进给精度;二是接触轮的回转精度,对于接触式砂带磨削将很大程度上影响着微量进给精度;三是接触轮材料的弹性变形,致使实际切深与理论切深不符,影响微量进给精度;四是车床进给机构、间隙影响微量进给精度。 由于以上四个因素的存在,影响微量进给精度,所以工件尺寸精度的保证受到影响,为此需从上述四个方面采取措施,提高微量进给精度,进而提高工件尺寸精度。
(2) 工艺系统刚度。在加工各部位工艺系统刚度不等的条件下,所加工的工件必然产生相应的轴向形状误差,影响尺寸精度。如实验中对细长轴的磨削,在工件两端时,工艺系统刚度较高影响较小,但在工件中段工件刚度很低,会产生较大的误差影响。
(3) 测量误差。提高测量精度就必须减少测量误差,以求获得最真实的结果。因此,一方面合理选择测量工具或测量方法,另一方面采用多次重复测量,尽可能减少测量误差。
3 圆度误差研究与分析
3.1 圆度误差测量
(1) 测量原理
砂带磨削后对工件拟采用分度头测量圆度误差,用游标原理对线进行读数。
采用极坐标测量半径法。利用分度头将圆周等分为24个测量点。当工件每转过一个360°/24角时,由千分指示表读出该点相对某一半径R的偏差△ri,采用最小二乘圆法评定圆度误差。即以实际轮廓上各点到某圆周上的距离平方为最小时的圆心为理论圆心,称最小二乘圆[9,10],最小二乘圆是唯一的,用公式表示为:
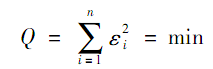
式中:εi为被测圆上各点到最小二乘圆之径向距离
设测量中心为O1,最小二乘圆圆心O(a,b),半径R,且O1O = e,且令
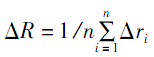
则:
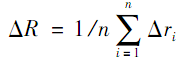
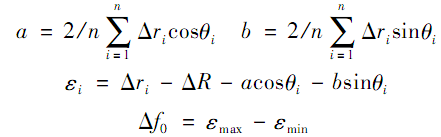
式中:△ri(i = 1,2,3,……,n)为各测量点测得半径方向的变化量;
θi(i = 1,2,3,……,n)为各测量点分度的角度值(θi= 360 /24 = 15°) ;
△f0为圆度误差
(2) 测量数据及结果
随机抽取5个工件测量圆度误差,测量时将被测工件顶在分度头两顶尖之间,每个工件上分别选择工件刚度强的截面1和刚度弱的截面5(见表2中图)各进行一次数据采集。据上述测量原理编写程序对测量数据进行处理,结果见表2。
表2 细长轴开式砂带磨削圆度误差实验数据 (单位:m)
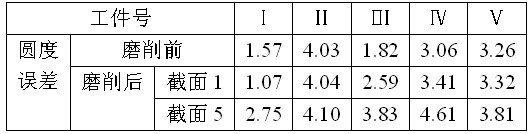
3.2 影响圆度误差的因素
(1) 主轴回转精度
通过Taylor圆度仪检测,工件表面产生棱圆度误差的主要原因是机床的主轴回转精度不高引起。因此提高机床主轴回转精度是降低圆度误差的主要措施。
(2) 零件定位误差
在砂带磨削试验中,工件以两端中心孔定位,主轴端采用固定顶尖与鸡心卡头,尾端采用活顶尖。由于活顶尖轴承间隙的影响,降低了顶尖的刚度,产生定位误差,进而影响圆度误差[10]。
两个顶尖和工件上的两个中心孔本身精度以及它们之间的位置精度对工件回转精度有重要影响。工件上两个中心孔本身有形状误差时,用其定位对零件外圆进行磨削时,使工件瞬时回转轴线位置变动,产生椭圆度 工件上两个中心孔有同轴度误差时,也同样会影响零件加工时的回转精度,产生圆度误差和直线度误差,并影响尺寸精度和圆柱度。
(3) 砂带接触轮的形状误差及回转精度
对于接触式砂带磨削,砂带与工件呈线性接触,因此砂带的支撑体、接触轮的形状误差(圆度误差和径向跳动)直接影响被加工工件的圆度误差。当接触轮材料较硬时影响较大,较软时由于材料弹性变形大,对圆度误差的影响有所减小。从表2的数据可以看出,工件车削后采用砂带磨削,部分圆度误差增大,其主要原因就是由于接触轮形状误差和接触轮偏心所致。
(4) 实验装置中电机转速在600rpm左右,而开式砂带所需转速为3-5rpm,因此设计采用涡轮减速器加齿轮减速器进行降速,此装置装在机床的溜板箱上,电机和减速器产生的微小振动会传给砂带接触轮,但由于砂带磨削具有“弹性磨削”的特点,因此振动带来的影响将大大减小。
4 结 论
实验表明,在细长轴的加工问题上,当车削完成后直接进行砂带磨削提高加工精度是有效的。砂带磨削对工件前道工序产生的锥度、腰鼓度现象能起到部分消除的作用。砂带磨削后工件的尺寸精度和圆度误差均可达5-7级以上,较前道工序精度提高1-2级以上。为了更好地提高加工精度砂带磨削时应注意以下几点[11,12]。
(1) 优化机床进给机构,提高微量进给精度。普通机床最小微进给在10-20μm,某些数控机床的微进给可控制到5μm,这对利用现有机床进行砂带磨削提高精度产生一定影响。 因此改进传统进给系统的结构形式,优化机床进给机构,是提高微量进给精度措施之一。
(2) 提高机床主轴回转精度、降低圆度误差。一般情况可用调整轴承间隙和采用高精度轴承来降低主轴径向跳动和端面跳动,在精密机床中采用液体或气体静压轴承来提高主轴回转精度。
(3) 确保接触轮系统的制造精度和装配精度。当砂带装置的接触轮采用橡胶接触轮时,由于橡胶材料的弹性变形,致使磨削时的实际切深与理论切深不符,从而影响尺寸精度。因此要获得良好的尺寸精度,必须合理选用接触轮材料,采取定量控制接触轮的变形量,从而提高加工精度。
(4) 提高工艺系统刚度,特别是最薄弱的地方。对细长轴的加工,关键是提高工件的刚性,可以采用中心架、跟刀架等工艺措施。
(5) 精加工时,要用合金顶尖研磨工件中心孔,同时保证机床上两个准确形状的固定顶尖调整在同一轴线上。
参考文献
[1] [美]法拉戈 F T.美国磨削技术[M].李长林,译.北京:机械工业出版社,1991.
[2] 李伯民.实用磨削技术[M].北京: 机械工业出版社,1996.
[3] 李虹.砂带磨削在普通车床上的应用研究.华北工学院学报,2000,21(1):78~81.
[4] 黄云,黄智.砂带磨削的发展及关键技术[J].中国机械工程,2007,18(9):2263~2266.
[5] 王维朗,潘复生.砂带磨削技术及材料的研究现状和发展前景[J].材料导报,2006,20(2):106~108.
[6] 邓玉平.砂带磨削在机械加工中的应用[J].水利电力机械,2007,29(11) : 85~86.
[7] 李虹.开式砂带磨削参数对表面粗糙度影响的分析与优化[J].机械设计与研究,2011, 29(11): 85~86.
[8] 谢国如.基于CA6140 车床砂带磨削不锈钢轴的研究[J].金刚石与磨料磨具工程,2004,144( 6) : 65~67.
[9] 李虹,李伯民.圆度误差测量及误差分析[J].山西机械,2000,106(1) : 44 ~ 45.
[10] 覃爱梅,黎良新.用分度头测量圆度误差的数据处理[J].装备制造技术,2011,(18) 11: 67-68.
[11] 王启平.精密加工工艺学[M].北京: 国防工业出版社,1990.
[12] 陈琦,崔瑞明.磨削加工精度分析及提高方法[J].金属加工(冷加工),2011,32(10):50~52.
作者简介:李虹( 1966- ) ,女,副教授,主要研究方向:机械设计与制造、精密加工、工程图学、CAD,发表论文20余篇,省级获奖1项。
转载自《机械设计与研究》第29 卷第1期(2013年2月)
基金项目: 国家自然科学基金资助项目( 51275486)